Filtration Efficiency Metrics: What You Need to Know
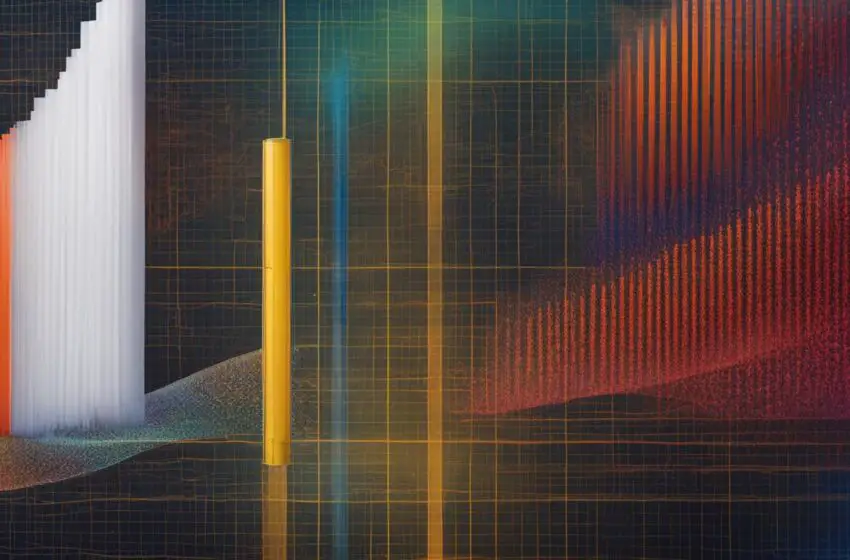
Filtration efficiency testing is a critical process that determines how well a material filters out particles, bacteria, and viruses. It is essential for manufacturers to ensure their products provide the necessary level of protection. Different types of efficiency testing are conducted to evaluate the performance of materials in specific environments.
Key Takeaways:
- Filtration efficiency testing is crucial for assessing the performance of materials in filtering out particles, bacteria, and viruses.
- There are different types of efficiency testing, including bacterial filtration efficiency (BFE), particle filtration efficiency (PFE), and viral filtration efficiency (VFE).
- Efficiency testing helps manufacturers select the right materials for their products and ensure the safety of individuals in various industries.
- ASTM standards provide guidelines for classification and rating of filtration efficiency, with ASTM Level Three offering the highest level of protection.
- Proper filtration efficiency testing is essential for choosing the right personal protective equipment (PPE) and preventing the transmission of diseases and harmful particulates.
Understanding Filtration Efficiency Testing
Filtration efficiency testing is a crucial process used to assess the ability of materials in personal protective equipment (PPE) to filter out particles. This testing is especially important for products like face masks, coveralls, and medical clothing, which play a vital role in protecting individuals from various hazards.
There are three primary types of filtration efficiency testing:
- Bacterial Filtration Efficiency (BFE)
- Particle Filtration Efficiency (PFE)
- Viral Filtration Efficiency (VFE)
BFE testing measures the material’s ability to filter out bacteria, PFE testing evaluates its effectiveness against particles of different sizes, and VFE testing assesses its capability to block viruses. These tests are performed following specific ASTM standards, ensuring consistent and reliable results across different laboratories.
For medical-grade face masks, ASTM F2100 is a commonly used standard that defines the filtration efficiency requirements. Adhering to such standards helps manufacturers ensure that their products provide the necessary level of protection to individuals in diverse environments.
With the results of filtration efficiency testing, manufacturers can confidently assert that their PPE products meet the required standards and offer reliable protection. These tests enable companies to make informed decisions when selecting suitable PPE for different scenarios, ensuring the safety and well-being of individuals.
The Importance of Filtration Efficiency Testing
Filtration efficiency testing is essential for ensuring the highest level of protection provided by personal protective equipment (PPE) against diseases, viruses, and harmful particulates. These tests play a crucial role in hazard prevention, maintaining the safety of wearers, and protecting the skin from potential harm. By conducting thorough filtration efficiency tests, manufacturers can evaluate the ability of their products to filter out microscopic elements and prevent their passage through the fabric barrier.
During the testing process, the effectiveness of PPE products in preventing the transmission of diseases is determined. These tests provide manufacturers and users with valuable information about the product’s ability to offer the necessary level of protection against various hazards. Additionally, filtration efficiency testing plays a vital role in evaluating the overall protective capabilities of items such as coveralls, gowns, and medical clothing, ensuring that the wearer is shielded from potential harm.
Filtration efficiency testing holds significant importance across multiple industries, including medical, dental, veterinary care, manufacturing, construction, and energy sectors. These industries rely on PPE products to safeguard employees and maintain a safe work environment. By rigorously testing the filtration efficiency of these products, companies can effectively prevent the transmission of diseases and protect individuals from hazardous particles and substances.
In conclusion, filtration efficiency testing is an indispensable process that guarantees the optimal performance of PPE products. These tests not only contribute to hazard prevention but also ensure the protection of individuals in various industries. By adhering to stringent testing standards, manufacturers can provide reliable and effective PPE products that prioritize the safety and well-being of individuals.
Industry | Importance of Filtration Efficiency Testing |
---|---|
Medical | Preventing the spread of diseases and protecting healthcare workers and patients |
Dental | Maintaining a sterile environment and safeguarding dental professionals and patients |
Veterinary Care | Protecting veterinary staff and animals from potential infections |
Manufacturing | Ensuring employee safety and preventing the release of harmful particles into the environment |
Construction | Shielding workers from hazardous substances and maintaining a secure work environment |
Energy | Protecting workers from harmful chemicals, fumes, and other occupational hazards |
Industries Using Filtration Efficiency Testing
Filtration efficiency testing plays a crucial role in various industries that require specific levels of protection. These industries include medical fields, dental fields, veterinary care, manufacturing, construction, industrial, and energy sectors. In these sectors, it is essential for manufacturers of personal protective equipment (PPE) to utilize filtration efficiency testing to determine the effectiveness of their products.
In the medical fields: Filtration efficiency testing is vital for medical-grade face masks, surgical gowns, and other PPE used in hospitals, clinics, and research facilities. These tests ensure that the materials used provide the necessary protection against harmful particles, bacteria, and viruses.
In the dental fields: Dental professionals rely on filtration efficiency testing to assess the performance of face masks and other PPE used during various procedures. It helps them select products that offer the highest level of protection against potential aerosolized pathogens.
In veterinary care: Filtration efficiency testing is crucial in veterinary clinics and animal hospitals. It helps ensure that PPE used by veterinary professionals offers adequate protection against potential zoonotic diseases and other microbial threats.
In manufacturing: Many manufacturing industries, such as pharmaceuticals, biotechnology, and electronics, require strict contamination control measures. Filtration efficiency testing ensures that cleanrooms, protective clothing, and other PPE meet the necessary standards to prevent contamination.
In construction and industrial sectors: Filtration efficiency testing is important in construction and industrial settings where workers may be exposed to hazardous particles and chemicals. PPE, including respiratory masks and protective clothing, undergo filtration efficiency testing to verify their ability to protect workers from harmful substances.
In energy sectors: Filtration efficiency testing is also relevant in the energy sector, particularly in nuclear power plants and oil refineries. PPE used by workers in these sectors undergoes rigorous testing to ensure their ability to protect against hazardous airborne contaminants.
By conducting filtration efficiency testing, PPE manufacturers can provide products that meet the specific requirements of these industries. Furthermore, companies in these sectors can select PPE based on their individual ratings, ensuring the safety and well-being of their employees in various work environments.
Browse the table below for a summary of industries using filtration efficiency testing:
Industry | Applications |
---|---|
Medical Fields | Face masks, gowns, medical clothing |
Dental Fields | Face masks, protective eyewear |
Veterinary Care | Animal clinic PPE |
Manufacturing | Cleanrooms, protective clothing |
Construction | Respiratory masks, protective clothing |
Industrial | Respiratory masks, protective clothing |
Energy Sectors | Respiratory masks, protective clothing |
Types of Filtration Efficiency Testing
When it comes to filtration efficiency testing, there are three primary types that are commonly used to assess the performance of materials. These tests play a vital role in determining the effectiveness of products in filtering out specific elements. Let’s take a closer look at the three types of filtration efficiency testing:
Bacterial Filtration Efficiency (BFE) Testing
Bacterial filtration efficiency (BFE) testing is designed to evaluate how well a material filters out bacteria. It measures the percentage of bacteria that are blocked by the material, with higher percentages indicating better filtration performance. BFE testing is particularly important in industries where protection against bacteria is critical, such as healthcare and food processing.
Particle Filtration Efficiency (PFE) Testing
Particle filtration efficiency (PFE) testing is used to assess the material’s ability to filter out particles of different sizes, including non-viable particles. This type of testing helps determine the effectiveness of products in blocking dust, pollen, and other airborne particles. PFE testing is crucial in industries where worker safety is a priority, such as construction and manufacturing.
Viral Filtration Efficiency (VFE) Testing
Viral filtration efficiency (VFE) testing evaluates how well a material filters out viruses. It is similar to PFE testing but specifically focuses on the material’s performance against viral particles. VFE testing is especially relevant in industries where protection against viral transmission is essential, such as healthcare and disease control.
All three types of filtration efficiency testing are conducted according to rigorous standards set by organizations like ASTM. These standards ensure consistency and reliability across different laboratories, allowing for accurate comparisons of filtration performance. Manufacturers can use the results of these tests to provide ratings for their products based on their filtration efficiency performance, helping customers make informed decisions.
The Role of ASTM Standards in Filtration Efficiency Testing
ASTM standards play a crucial role in filtration efficiency testing, ensuring that manufacturers adhere to consistent guidelines to provide reliable and effective personal protective equipment (PPE). Among the various ASTM standards, one of the most commonly referred to in filtration efficiency testing is ASTM F2100. This standard specifically classifies PPE products, particularly face masks, into different levels based on their filtration efficiency and intended use.
ASTM Level One masks are suitable for basic medical procedures with no fluid exposure. They offer a certain level of filtration efficiency and provide a basic level of respiratory protection.
ASTM Level Two masks offer moderate protection against fluid exposure and are commonly used in medical and dental settings where there may be a higher risk of exposure to bodily fluids.
ASTM Level Three masks provide a high level of protection against fluid spray or exposure. They are commonly used in surgical procedures and environments where there is a significant risk of exposure to hazardous liquids.
In addition to these levels, N95 masks, which provide a higher level of protection, are typically worn in situations with an expected exposure to aerosol-transmitted diseases like COVID-19 or tuberculosis.
By following ASTM standards, manufacturers can provide PPE products that offer the appropriate levels of protection for different environments, ensuring the safety and well-being of individuals.
ASTM Level | Protection Level | Intended Use |
---|---|---|
Level One | Basic | Low fluid exposure |
Level Two | Moderate | Moderate fluid exposure |
Level Three | High | High fluid exposure |
Conclusion
Filtration efficiency testing is paramount in ensuring the efficacy and performance of personal protective equipment (PPE) products. These tests assess how proficiently a material filters out particles, bacteria, and viruses, enabling manufacturers to offer products that provide the necessary level of protection. Various types of filtration efficiency testing, including Bacterial Filtration Efficiency (BFE), Particle Filtration Efficiency (PFE), and Viral Filtration Efficiency (VFE), evaluate material performance in specific environments.
ASTM standards play a crucial role in filtration efficiency testing by providing manufacturers with guidelines and ensuring consistency throughout the industry. Adhering to these standards allows companies to deliver PPE products that safeguard individuals in a range of industries, such as medical, dental, manufacturing, and construction. Filtration efficiency testing is instrumental in maintaining safety and preventing the transmission of diseases and harmful particulates.
By prioritizing filtration efficiency, PPE manufacturers can confidently provide high-quality products that meet industry standards and protect wearers. Whether it’s face masks, coveralls, or medical clothing, filtration efficiency testing enables reliable and effective hazard prevention, promoting the safety of individuals across various sectors. As we continue to face ongoing health challenges, filtration efficiency remains a critical factor in safeguarding against potential risks.
FAQ
What is filtration efficiency testing?
Filtration efficiency testing is a process used to determine how well a material filters out particles, bacteria, and viruses. It helps manufacturers ensure that their products provide the necessary level of protection in different environments.
Why is filtration efficiency testing important for personal protective equipment (PPE)?
Filtration efficiency testing is especially important for PPE like face masks, coveralls, and medical clothing. It helps manufacturers determine the effectiveness of their products in preventing the transmission of diseases and maintaining the safety of wearers.
What are the types of filtration efficiency testing?
The three common types of filtration efficiency testing are bacterial filtration efficiency (BFE), particle filtration efficiency (PFE), and viral filtration efficiency (VFE). BFE tests measure how well a material filters out bacteria, PFE tests measure its ability to block particles of different sizes, and VFE tests assess its effectiveness against viruses.
What industries use filtration efficiency testing?
Industries that require specific levels of protection, such as medical fields, dental fields, veterinary care, manufacturing, construction, industrial, and energy sectors, use filtration efficiency testing to ensure the effectiveness of PPE products.
What are the ASTM standards used in filtration efficiency testing?
The most commonly referred to ASTM standard in filtration efficiency testing is ASTM F2100. This standard classifies PPE products, particularly face masks, into three levels based on their filtration efficiency and the intended use.
How does filtration efficiency testing contribute to hazard prevention and skin protection?
Filtration efficiency testing plays a critical role in maintaining safety and preventing the transmission of diseases and harmful particulates. It ensures that PPE products provide the necessary level of protection and perform as designed in different work environments.